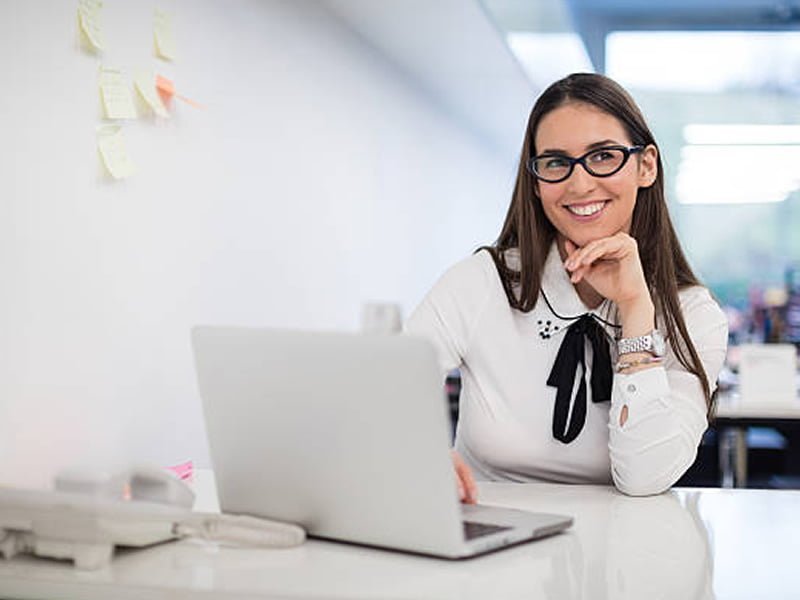
The Lean Six Sigma principles are like every other proposition that guides human reasoning and motivates them to take action on what they believe to be in sync with their chosen direction. Indeed, Lean Six Sigma is seen to be one of the most effective tools used for process improvement in project management.
For organisations that adopt the Lean Six Sigma methodology, process owners have been taught to apply the Lean Six Sigma principles to achieve work efficiency among staff and managers.
The ultimate goal for the improvement team is to streamline the workflow so that wasteful tasks are eliminated. This helps to ensure that processes are run efficiently with fewer, and invariably, closer to zero defects with the proper implementation and use of Lean Six Sigma principles.
MakeWay Global, not only teaches these core elements – Lean Six Sigma principles, Lean Six Sigma tools, Lean Six Sigma methodology and so on – in the classroom, but also provides free post training coaching services towards the demonstration of real life improvements in the work environment.
To achieve this, continuous improvement consultants and coaches, like those at MakeWay Global, offer the Lean Six Sigma training to organisations. This training with the company’s employees enforced with the knowledge of Lean Six Sigma principles, impacts their mind-sets towards the adoption of a new work culture that promotes the optimisation of production and service delivery processes.
It is worth noting, that the Lean Six Sigma training is in varying levels. Since this training aims towards changes in ideology, development of new skills and continuous improvement among workers, it must remain gradual.
Nevertheless, all Lean Six Sigma levels serve the same ultimate purpose – efficiency and optimisation of production and service delivery processes.
The process of optimisation within any organisation is only possible when the Lean Six Sigma principles are appropriately applied. In this article, we share the six (6) highly effective Lean Six Sigma principles that everyone interested in this subject needs to know about. These are:
The concept of “Customer first” is the ultimate rule for any business success. A lack of demand for an organisation’s products or services would indicate that there are no customers to accept what the organisation is offering. The truth is, no company survives or thrives without its customers.
With Lean Six Sigma training and effective knowledge and implementation of the Lean Six Sigma principles, staff and managers are instilled with the emphasis that the company’s success and profitability can only come through customer satisfaction. There is also the need to understand that there are both internal and external customers – the recipient of the output of a process is referred to as a customer.
There are lots of Lean Six Sigma pdf books that teach about customers’ satisfaction and how it gets impacted without the effective implementation of Lean Six Sigma principles. A number of these emphasise the point that listening to customers’ demands or complaints is one of the keys to business success in the corporate world.
A value stream helps one to identify and understand how the work gets done. One of the things that should be taught at a Lean Six Sigma training event and during the Lean Six Sigma principles exercise is how to construct a value stream map. This is typically a flowchart that is enhanced with the inclusion of how people, material and other resources move within the process flow.
Lean Six Sigma ensures that the process activities are well mapped out to identify any tasks that seem to occupy space and takes time without any value-add significance. A knowledge of the value stream is one of the most effective Lean Six Sigma principles that aid the identification of the causes of defects in a work process.
Certain Lean Six Sigma pdf books describe value stream mapping as a way to visualise work and guide the quality of products or services. MakeWay Global emphasises these aspects as a response to the question, what is Lean Six Sigma certification and why organisations that seek continuous improvement require it (thorough knowledge and proper use of the Lean Six Sigma principles).
One of the reasons anyone needs to be Lean Six Sigma certified is that it teaches the essential elements of value stream mapping. The approach to value stream mapping and quality control with the Lean Six Sigma methodology is second to none.
Similar to the way that Lean Six Sigma levels vary from one belt level to another, an organisation’s workflow processes can also be seen as a staged flow. So, it is essential that one can manage, improve and smoothen the process flow continually. One cannot improve a process without knowing the steps that lead to one another.
( image for reference )
Often, managers document the workflow to better grasp the stream of tasks that flow through the process of generating an output. The emphasis here is that it is important to review the workflow on a continuous basis, to know and differentiate which tasks add value from those that do not. The ones that do not add value are essentially, waste.
A good practical knowledge of Lean Six Sigma and its principles helps to identify which activities are waste, in a bid to eliminate them. This is why well-meaning continuous improvement consultants encourage managers to become Lean Six Sigma certified, as a way of galvanising efforts within an organisation to practise its tenets.
One key factor of Lean Six Sigma principles is that the analysis and evaluation of a problem situation is based on the use of real data. To effect any changes to an output delivery process, one should consider the effect of the variables, using the actual data involved.
( credit – IT Business Partners, AU )
Lean Six Sigma Green Belt certificate holders should be able to do this effectively because of their data analysis and evaluation skills. The collection of data from customer feedback, for example, will help with the analysis of the causes for customer complaints.
The Lean Six Sigma premise seeks to communicate the understanding that those closest to the actual work activities are indeed the subject matter experts. Hence, there needs to be a level of trust that is placed upon employees towards identifying potential improvement areas. This calls for flexibility in management.
Lean Six Sigma allows for flexibility in several ways. It not only transforms the employees’ mind-sets about a positive workplace culture, but also helps them adapt to changes within the work environment. This is one of the Lean Six Sigma principles that calls for respect and trust for employees and their empowerment.
Lean Six Sigma adoption must be culturally propelled that the drive is for perfection – there is always room for improvement. The most important change in mind-set is the fact that all employees should always seek for opportunities to improve their current level of work.
People detest change. This means that employees will enjoy being comfortable with how an organisation runs a business, irrespective of loss and economic crisis. However, the Lean Six Sigma training can result in company-wide transformed views. It helps to communicate the company’s objective clearly and concisely.
This methodology invokes the best and effective modality that brings efficiency to any organisation while maintaining the standards of the Lean Six Sigma principles and their proper implementation. It ensures that every employee is trained on how to communicate with one another and external customers. Communication enables employees to know the recent workflow changes and how to adjust to latest developments.
******************
For the purpose of clarity… what is Lean Six Sigma certification? The certification proves that its bearer has been schooled on the tools and techniques to improve an organisation’s processes. Invariably, this seeks to assure acceptability of its products and services by the deemed recipient (the customer).
If any organisation would like its workers to understand workstream value, they ought to undergo the Lean Six Sigma training. MakeWay Global offers the three basic levels of training – the Yellow Belt, the Green Belt and the Black Belt.
The Lean Six Sigma Yellow Belt is the foundation level of this training. This level gives a basic knowledge of the methodology that enables participants to find and make improvements to their own work.
[youtube v=”xc0pYSiIod8″]
The Lean Six Sigma Yellow Belt, however, does not take the lead in the company’s improvement projects, which is where the Lean Six Sigma Green Belt comes in. A person trained to lead a team for an improvement project, would have been practically taught the problem solving cycle that aids the process improvement work within their team.
The Lean Six Sigma Green Belt holder, after undertaking a number of improvement projects, either as a team member or team leader, may also look to attaining the Lean Six Sigma Black Belt certification. The Lean Six Sigma Black Belt certificate holder may now lead on company level improvement projects.
In conclusion, all these six principles are the key factors that describe the underlying fabric of Lean Six Sigma. We must learn to make customers our priority and eliminate activities that do not add value to their requests. Employees working in the same direction allow for greater productivity and a better outcome and that’s where the Lean Six Sigma principles come into enforcement.
Without the appropriate knowledge on the Lean Six Sigma principles, it would become highly difficult and risky to implement the lean tools for better productivity, wouldn’t you agree?
Sign up for our newsletter and get access to a broad range of training information and materials which will help to improve your business processes and career prospects.
After payment, please send an email to connect@makewayglobal.com with (Name, Email Address and Telephone Number) or call +44 20 3858 3600.
Your confirmation will be e-mailed to you. Review it for accuracy and bring it with you to the training venue. Your confirmation verifies your course registration. Seating is limited. Refreshments and training resource kits are included in training fees.
Transfers are permitted one time only within the calendar year. Transfer requests must be submitted in writing via e-mail no later than 7 business days before the programme start date. You may transfer into another training event that will be held before September 30, 2027. If you are unable to send a replacement, you forfeit your registration fee. If you are unable to attend the programme to which you transfer, you may send a replacement. All transfers and cancellations must be made in writing to connect@makewayglobal.com